無氧銅杆和低氧銅杆加工(gōng)性能(néng)的比較
- 分(fēn)類:行業新(xīn)聞
- 作(zuò)者:
- 來源:
- 發布時間:2019-01-09
- 訪問量:0
【概要描述】連軋低氧銅杆的制造方法較多(duō),常見 下遊工(gōng)序對銅杆的主要加工(gōng)要求 的有(yǒu)SCR法、Properzi 法和Contirrod法 歸結起來有(yǒu)三個方面:拉制性能(néng)、退火 等 ,其特點是金屬在豎爐中(zhōng) (個别采用(yòng)電(diàn)爐性能(néng)、表面質(zhì)量。
無氧銅杆和低氧銅杆加工(gōng)性能(néng)的比較
【概要描述】連軋低氧銅杆的制造方法較多(duō),常見 下遊工(gōng)序對銅杆的主要加工(gōng)要求 的有(yǒu)SCR法、Properzi 法和Contirrod法 歸結起來有(yǒu)三個方面:拉制性能(néng)、退火 等 ,其特點是金屬在豎爐中(zhōng) (個别采用(yòng)電(diàn)爐性能(néng)、表面質(zhì)量。
- 分(fēn)類:行業新(xīn)聞
- 作(zuò)者:
- 來源:
- 發布時間:2019-01-09
- 訪問量:0
連軋低氧銅杆的制造方法較多(duō),常見 下遊工(gōng)序對銅杆的主要加工(gōng)要求 的有(yǒu)SCR法、Properzi 法和Contirrod法 歸結起來有(yǒu)三個方面:拉制性能(néng)、退火 等 ,其特點是金屬在豎爐中(zhōng) (個别采用(yòng)電(diàn)爐性能(néng)、表面質(zhì)量。
用(yòng)感應電(diàn)爐 )熔化後,銅液通過保溫 爐、溜槽、中(zhōng)間包,從澆管進入以鑄 ;
一 ,拉 制性能(néng) 輪和鋼帶 (或雙鋼帶 )形成的封 閉金 銅杆 的拉制性能(néng)跟多(duō)種 因素相屬模腔,采用(yòng)較大的冷卻強度 ,連續 ; 關,如雜質(zhì)含量及分(fēn)布、氧含量及分(fēn)的形成鑄坯之後再進行多(duō)道次軋制, i 布、生産(chǎn)工(gōng)藝控制等。當銅杆性能(néng)良生産(chǎn)的銅線(xiàn)杆為(wèi)加工(gōng)态組織,含氧量 好時,以拉制中(zhōng)0. 4mm$ 0中(zhōng)0. 2mm為(wèi)一 般為(wèi)200~400ppm之間。無氧銅杆 例,無氧銅杆和低氧銅杆斷線(xiàn)率相差
國(guó)内基本全部為(wèi)Upcast 上引連鑄法生 不大,但斷線(xiàn)原因有(yǒu)所不同。
産(chǎn),金屬在感應電(diàn)爐 中(zhōng)熔化後通過石 1 .熔化方式對S等雜質(zhì)的影響 墨模進行上引連續鑄造,之後進行冷 j 在制造過程中(zhōng),應嚴格控制電(diàn)解
軋或冷拉加工(gōng),生産(chǎn) 的銅線(xiàn)杆多(duō)為(wèi)鑄 銅的雜質(zhì)含量。由于連鑄連軋工(gōng)藝通 造态 或冷加工(gōng) 态組織 ,含氧 量一般 為(wèi) 常采用(yòng)豎 爐熔 化 ,在 可(kě)燃氣體(tǐ) 的作(zuò) 用(yòng) 2 0ppm以下。由于兩種制造工(gōng)藝不 同, 下 ,通過 氧化和 揮發作(zuò) 用(yòng) ,可(kě)一定 程 銅杆在組織結構、氧含量及分(fēn)布、雜 度減少部分(fēn)雜質(zhì)進入銅液 ,在正常生 質(zhì)的形式及分(fēn)布等諸多(duō)方面有(yǒu)較大差 産(chǎn)中(zhōng),S因大量存在于銅闆表面,可(kě)減 蓑 {遺鎊适甜低氯銅 和 I } 運鐮 無氧鍛杆在制造 方式 々不同之處 原料電(diàn)解銅品質(zhì) 一般 較函 熔化 方式 豎爐、個别采用(yòng)感應 電(diàn)爐 感應電(diàn)爐 熔融金屬轉運方式 保溫爐、溜槽、中(zhōng)間包 連體(tǐ)感應電(diàn)爐内流動 鑄造 方式 輪帶金屬模 内或雙帶金屬模 内 石墨模 内 軋制 方式 熱軋 不軋制或冷軋 酸洗 方式 酒精(jīng) 無酸洗
38 資源再生 201 0 1 2少約一半。Zn、C r 、Mn、Cd等元素 亦可(kě)在氧化燃燒中(zhōng)去除 ,因而連鑄連 軋法對原料要求相對低一些。
上引連鑄無氧銅杆 ,由于是采用(yòng) 感 應 電(diàn)爐熔 化 ,沒 有(yǒu)氧 化燃燒過 程 ,電(diàn)解銅闆表面的 “ 銅綠”、 “ 銅豆”
基本都熔入到銅液中(zhōng)。其中(zhōng)熔入的S對 無氧銅杆塑性影響極大,它在銅中(zhōng)生 成硬而脆的Cu, S,增加拉絲斷線(xiàn)率。
其形成 反應 為(wèi) :
6Cu+SO,=2Cu, O+Cu, S
同時 由于上 引連鑄 法爐體(tǐ)容 量有(yǒu) 限和潛流式的特點 ,當某塊 電(diàn)解銅闆 雜質(zhì)含 量波動 時 ,對結 晶器 口周 圍銅 液 成分(fēn) 會有(yǒu)一 定的影 響 ,相 比連鑄 連 軋 工(gōng)藝 對 電(diàn)解銅 闆 雜質(zhì) 含量 和穩定 性 要 求更 高。
2.制造過程中(zhōng)雜質(zhì)的進入 在生産(chǎn)過程 中(zhōng) ,連鑄連 軋工(gōng)藝 需通過保溫爐、溜槽、中(zhōng)間包轉運銅 液 ,相對容易造成耐火材料的剝落,
熱軋制過程需通過軋輥 ,造成鐵質(zhì)的 脫落,這會給銅杆帶來外部夾雜。而 熱軋中(zhōng)皮上和皮下氧化物(wù)的軋入,會 給低氧杆 的拉 絲造成 不利的影響。
如圖1、圖2、圖3所示,分(fēn)别為(wèi)低氧 銅絲 0 40mm的拉斷試樣 ,經檢測 其 中(zhōng)含 Fe、C r 雜質(zhì) ,圖4為(wèi)低 氧銅 絲
0 20mm含A J 雜質(zhì)的斷 口電(diàn)鏡掃描 圖 。 圖 5為(wèi)低氧銅 絲 中(zhōng)0. 1 0mm斷 口 含耐火材料雜質(zhì)的掃描圖,圖6為(wèi)低氧 銅絲 O 1 0mm中(zhōng)含剝落的軋輥材料 H1 3雜質(zhì) 的斷口掃描 圖。
與此相 反 ,上 引連鑄 工(gōng) 藝的流程 較短,銅液的轉運是通過聯體(tǐ)爐 内潛 流式完成,對耐火材料的沖擊不大。
上引連鑄的結 晶過 程在石墨模 内進 行 ,完 全與氧 隔絕 ,後 續 也不進 行熱 SL) J u 工(gōng) ,可(kě)能(néng)産(chǎn)生的污染源較少,生 産(chǎn)過程中(zhōng)雜質(zhì)進入的機會較少,圖7、
圖8為(wèi)無氧銅絲中(zhōng)O 1
5mm中(zhōng)的Si 雜質(zhì) 的斷口掃描圖。
0、S兩種 元素 幾乎 不溶 于銅 ,會與銅形成高熔點脆性化合物(wù) ,對銅線(xiàn)杆生産(chǎn)過程有(yǒu)很(hěn)大影響。
3.氧在低氧銅杆和無氧銅杆中(zhōng)分(fēn)布形式及其影響氧含量對低氧銅杆的拉線(xiàn)性能(néng)有(yǒu)着明顯的影響 。 當加 工(gōng)成0. 4mm銅 線(xiàn)時,所得的數據,V形曲線(xiàn)表明,當氧含量增加到最佳值時 ,銅杆 的斷線(xiàn)率最低。這是因為(wèi)氧在與大部分(fēn)雜質(zhì)反 應的過程中(zhōng)都起到了清除器的作(zuò)用(yòng)。适度的氧還有(yǒu)利于去除銅液中(zhōng)的氫,生成水蒸汽溢 出,減少氣孔的形成 。最佳的氧含量為(wèi)拉線(xiàn)工(gōng)藝提供 了最好
的條件。
低氧銅杆 氧化物(wù) 的分(fēn)布 :在連續澆鑄中(zhōng)凝固的最初階段,散熱速率和均勻冷卻是決定銅杆氧化物(wù)分(fēn)布的主要 因素。不 均勻 冷卻 會 引起銅杆 内 部 結構本質(zhì) 上 的差 異 ,但後續 的熱 加 工(gōng) ,柱 狀 晶通 常會 遭到破 壞 ,使氧 化 亞銅顆粒細微化和均勻分(fēn)布。氧化物(wù) 顆粒聚集而産(chǎn)生的典型情況是中(zhōng)心爆 裂 ,圖9、10是 0. 40mm' f l ~氧銅絲 因 中(zhōng)心爆裂斷口的掃描圖。不均勻區(qū)域 在 外 力作(zuò)用(yòng) 下 ,氧化 物(wù)顆 粒 的變形 處 出現裂 紋造成 ,如 圖 1所示 ,深 色部 表2制造過程對 銅杆 質(zhì)量影響對 比 熔化 方式 豎爐 燃燒可(kě)去處部分(fēn)S雜質(zhì) , 感應 電(diàn)爐無法去 出S雜質(zhì) ,爐 爐容量大,爐内成份波動相對小(xiǎo) 容量小(xiǎo) ,爐 内成份易波動 熔融金屬轉運方式 耐火材料剝落、腐蝕 較少耐火材料剝落、腐蝕 鑄造方式 氧化粒子混入 上引時氣體(tǐ)難以排除,産(chǎn) 生氣孔、縮松 軋制方式 表面氧化物(wù)軋入 無 酸洗方式 表面氧化層剝落 無 圖1低氧銅絲 O40mm 1 000× 圖2低氧銅絲 O40mm 200X 一 圖3低氧銅絲 eO40mm 1000× 圖4低氧銅絲 0 20mm 800X 一 圖 5 恹氧銅絲 口0 1Omm耐火材料雜質(zhì) 圈6低氧銅絲 0 1 Omm軋輥H1 3剝落的雜質(zhì)
圖7無氧銅絲 0 15mmS 雜質(zhì) 圖8無氧銅絲 0 15mm Sl 雜質(zhì) 位為(wèi)氧化物(wù)區(qū)域,細裂紋總是從此類 區(qū)域産(chǎn) 生。 除氧化物(wù) 顆粒 分(fēn)布 的影響 外,具(jù)有(yǒu)較小(xiǎo)氧化物(wù)顆粒的銅杆顯示 出較好的拉線(xiàn)特性 ,較大的Cu O顆粒 容 易造成應 力集 中(zhōng)點 而斷 線(xiàn)。 圖1
2、
1
3為(wèi)中(zhōng)0. 49mm低氧銅絲Cu2 0顆粒造
3 9
吸
技(jì )術 n n 0 呦y
一 一 一 嗣1 2 Ol 49mm低氧銅絲2OOX 嚣1 3口O49mm低氧銅絲2oO× 圖1 4 O49mm低氧銅絲2O0×
圖15無氧銅杆 12 5mm試樣金相組織 成的斷頭試樣照片。圖1 4為(wèi)低氧銅絲 中(zhōng)0. 49mm斷裂初始裂 口的照片。
無氧 銅 含 氧 量 超 标 ,銅 杆 變 脆 ,延 伸 率 下 降 ,拉 伸 式 樣 斷 口顯 暗紅色,結晶組織疏松。當 [ 01 超過 8×1O 時,工(gōng)藝性能(néng)變差 ,表現為(wèi) 鑄造及拉伸過程中(zhōng)斷杆及斷線(xiàn)率急劇 增 高。這是 由于氧能(néng)與銅 生成 Cu, O脆 性相,形成Cu—Cu O共晶體(tǐ) ,以網狀 組織分(fēn)布在晶界上。這種脆性相硬度 高,在冷變形時将與銅基體(tǐ)脫離 ,導 40 資源再生201 0 / 2緻銅杆的機械性能(néng)下降 ,在後續加工(gōng) 中(zhōng)容 易造成 斷裂現 象。氧 含量 高還能(néng) 導緻無氧銅杆導電(diàn)率下降。因此,必 須嚴格控制無氧銅杆中(zhōng)氧的含量 ,從 而控制上引法連鑄工(gōng)藝及産(chǎn)品質(zhì)量 。
4. 氫的影響
在上引連鑄中(zhōng),氧含量控制較低,氧化物(wù)的副作(zuò)用(yòng)被大大降低了,但氫的 影響成為(wèi)較顯著的問題。氫在銅中(zhōng)的溶 解度很(hěn)大,熔融狀态的液體(tǐ)銅每1 O Og能(néng) 溶解6 3 c m。 氫,這比同一溫度固體(tǐ)狀态 銅中(zhōng)氫的溶解度大2~3倍。吸氣後熔體(tǐ) 中(zhōng)存在如下的平衡反應:
H2 0( g) =【 O】 +2【 H1
氣 孔及疏松 是在結 晶的過程 中(zhōng) ,氫從過飽和的熔液中(zhōng)析出并聚集而形 成 的。在 結 晶前 沿析 出的氫 又(yòu)可(kě)還原 Cu Of l i 生成水汽泡 。由于上引鑄造 的 特點是銅液 自上而下的結晶,形成的 液 穴形狀近 似錐 形。銅液 結 晶前 析 出 的氣體(tǐ)在上浮過程中(zhōng)被堵在凝固組織 内,結晶時在鑄杆内形成氣孔。上引 的含氣量少時,析出的氫存在于晶界 處 ,形成 疏松 ;含氣 量多(duō) 時 ,則聚集 成 氣孔 ,因此 ,氣孔 和疏松 是氧氣和 水蒸氣兩者形成的。據相關資料,當 [ H】 超過O 6 X 10 時 ,工(gōng)藝性能(néng)變差 ,
表現為(wèi)鑄造及拉伸過程中(zhōng)斷杆及斷線(xiàn) 率急劇增高。
氫 來 源 于 上 引 生 産(chǎn) 過 程 中(zhōng) 的 各 個 工(gōng) 藝 環 節 ,如 原 料 電(diàn)解 銅 的 “銅 綠”、輔助材料木(mù)炭潮濕、氣候環境 潮濕、石墨結晶器未幹燥等。因此熔 化爐中(zhōng)的銅液表面應覆蓋經烘烤的木(mù) 炭 ,電(diàn)解銅應盡量去 除 “銅綠 ”、“ 銅豆 ” , “ 耳朵 ” ,對 提高無氧 銅 杆質(zhì)量非常重要。
在連鑄連軋工(gōng)藝中(zhōng),往往采用(yòng)适 度控制氧含量 (200~300ppm )來控 制氫。反應式為(wèi):
Cu,0+H, =2Cu+ H, 0
由于銅液在鑄輪中(zhōng)由下而上結晶,銅液中(zhōng)的氧和氫所産(chǎn)生的水蒸氣很(hěn)容易 上浮跑出,銅液中(zhōng)的氫大部分(fēn)能(néng)被有(yǒu)效 去除,因而對銅杆的影響較小(xiǎo)。
三 退火性 能(néng) 在對銅 絲退火過程 中(zhōng),同等功率 和時間的情況下無氧銅杆的延伸率要 比低氧銅低1 5% ~30%。 因此。在 對銅線(xiàn)退火時,~定要區(qū)别材質(zhì)采用(yòng) 不 同 的退 火工(gōng) 藝 ,以保 證制 品的柔軟 性 。其 産(chǎn)生 的原 因在 以下 的金相 對 比 中(zhōng)得到較好解釋:
圖 1
5、 圖 1 6分(fēn) 别 是 無 氧 銅 杆 中(zhōng)1
2. 5mm和中(zhōng)8mm試樣。試樣組織 為(wèi)呈發散狀的粗大柱狀 晶,晶粒大小(xiǎo) 為(wèi)2~3mm。表面和内部隻有(yǒu)少量等 軸晶粒。圖17、圖18分(fēn)别是低氧銅杆 中(zhōng)8mm試樣的中(zhōng)部和邊緣組織。深棕 色 的相 是 一般 退 火 再 結 晶 相 , 白 色 的 是退 火 過 程 中(zhōng)生 成 的 孿 晶 相 。 一 般 孿 晶 相 大 小(xiǎo) 在 1 O~2O u m之 間 ,
而 深 棕 色 的相 在 2 5 u m左 右 。可(kě) 見 ,低氧 銅杆 由于經過 熱軋 ,所 以 其組織屬 熱變形組織 ,原來的鑄造 組 織 已經 破 碎 , 以再 結 晶 的 形 式 出 現 ;而 無氧銅杆屬鑄造 組織 ,晶粒 粗大 ,晶粒邊界少 ,由于再 結晶發 生在 晶粒 邊界和孿 晶交截 處附近 ,
因而 即使 通過拉制變形 。其晶邊相 對低氧銅杆還 是較少 ,所 以需要較 高的退火功率。
此外 ,低氧銅中(zhōng)的氧與雜質(zhì)元素 形成氧化物(wù),使雜質(zhì)元素從銅的固熔 體(tǐ)分(fēn)離出來,從而降低 了有(yǒu)害雜質(zhì)元 素對退火溫度、導體(tǐ) 電(diàn)阻與回彈角的 影響。而無氧銅 由于氧含量低 ,雜質(zhì) 元素依然以固溶形式和生成彌散析 出 相存于 銅 中(zhōng) ,導緻 無氧銅 的退 火溫 度 比低氧銅高。
四 表面 質(zhì)量 在生産(chǎn)諸如電(diàn)磁線(xiàn)等産(chǎn)品的過程
中(zhōng),對銅杆 的表面質(zhì)量亦提出要求。
需要拉 制後 的銅 絲表 面無 毛 刺、銅 粉 少 、不爛 線(xiàn) 、無油污 。并 通過 扭轉 試 驗測量表面銅粉的質(zhì)量和扭轉後觀察 銅杆的複原情況來判定其好壞。
在連鑄連軋工(gōng)藝中(zhōng),銅坯從鑄輪 出口~l J SL 機入口之間,溫度高,完全暴 露于 空氣 中(zhōng),使鑄坯表面形成較厚的氧 化層,約40 00 0~1 0 00 0 00 A,在軋制
圖1 7 8mm' L ~氧銅杆 試楫 金相 紹織 (中(zhōng)部 ) 圖18 8mm低氧t l o ] ' F 式柑盒相絹織 (邊緣 過程中(zhōng),随着軋輥的轉動,氧化物(wù)顆粒 軋入銅線(xiàn)表面。通常采用(yòng)酒精(jīng)或硫酸來 進行清洗,化學(xué)反應式為(wèi) :
2Cu,O+CO+H,=4Cu+CO,+H,O
2CuO+CO+H,:2Cu+CO,+H,O
由于銅 與氧化銅 的密度相 差較 大 ,故在 反應 後 ,表面膜 形成 破 裂和 孔隙,軋入較淺的氧化物(wù)顆粒部分(fēn)溶 解和脫落 ,在表面形成麻點、粗糙不 平 ,在 拉 絲時 形 成 麻坑 。 由于 Cu, O 是 高熔點 脆性 化合 物(wù) ,對于 軋入較 深 的Cu, O,當成條狀的聚集物(wù)遇模具(jù) 拉伸時 ,就會使銅杆外表面 産(chǎn)生毛 刺,給後續的塗漆造成麻煩。而上 引連鑄 工(gōng)藝制造 的無氧銅 杆 ,由于鑄造和冷卻完全與氧隔絕 ,後續亦無熱軋過程 ,銅杆表面無軋入 表面 的氧 化物(wù) ,質(zhì)量 較好 ,拉 制後 銅 粉少、不爛線(xiàn),上述問題較少存在。
五 .結論 連 鑄連軋低氧銅杆 和上 引連鑄 無 氧 銅 杆 在 制造 方 式 上 的不 同 弓1 起 兩 者 在 組 織 結 構 、 氧 含 量 及 分(fēn) 布 、雜質(zhì)存在 方式和 氫含 量等諸 多(duō)方面 的不同 ,從而決 定 了兩者在使 用(yòng)特 性上 的不同。
1 .連鑄連軋采用(yòng)豎爐熔化,具(jù)備較 大爐容量 ,對 電(diàn)解銅品質(zhì)的要求相對低 一 些,上引連鑄工(gōng)藝對原料要求較高
2.連鑄連軋工(gōng)藝在後續澆鑄、熱軋等工(gōng)序會将雜質(zhì)和氧化物(wù)帶入銅 杆 ,給拉制帶來較大弊端,上引連鑄 工(gōng)藝無 此類問題 ;
3.氧 含量和氧 化物(wù) 的分(fēn)布 對低氧 銅杆的拉制性能(néng)有(yǒu)明顯影響 ,而無氧 銅杆對該問題較容易控制;
4.氫對無氧銅杆的拉制性能(néng)影響 較大 ;
5.組 織結構 、雜質(zhì) 的存在 方式、雜質(zhì)種類的不同導緻低氧銅杆 的退火 性能(néng)明顯好于無氧銅杆 ;
6.由于熱軋時表面氧化層的軋入 ,低氧銅杆的表面質(zhì)量明顯低于無 氧銅杆。
掃二維碼用(yòng)手機看
相關資訊
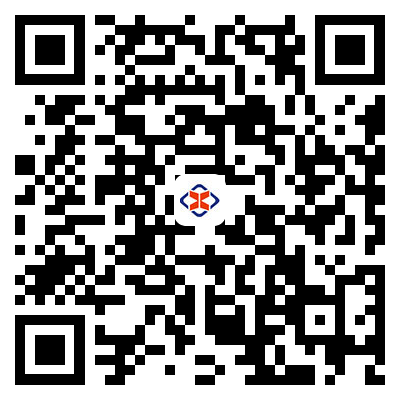
版權所有(yǒu) © 2021 鄭州恒天銅業有(yǒu)限公(gōng)司 京ICP證000000号 營業執照
網站建設:中(zhōng)企動力 鄭州 本網站已支持IPV6